Breakthrough High-Entropy Alloy Coatings Boost Hardness, Wear, and Corrosion Resistance for Industrial Applications
September 24, 2024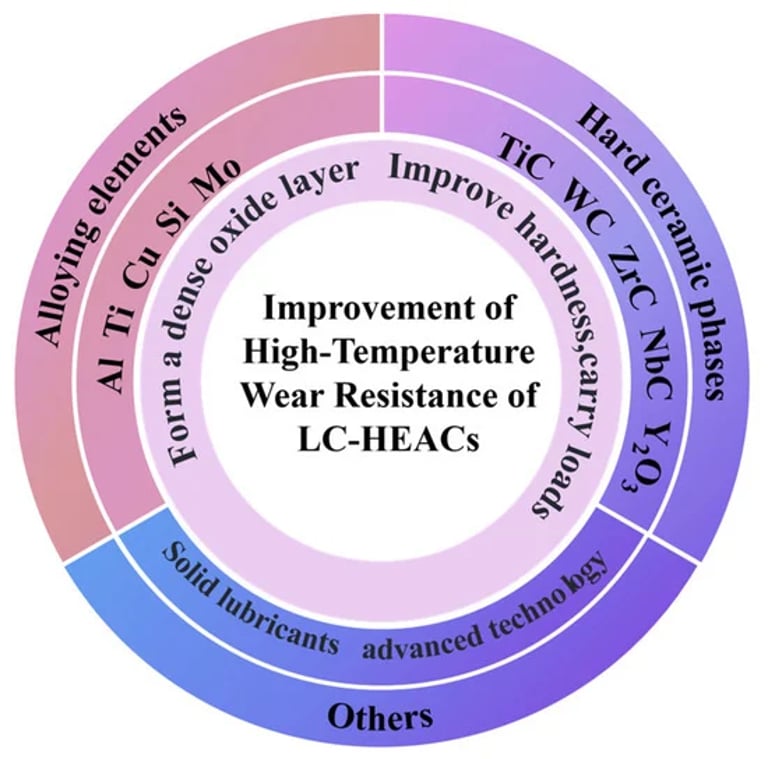
Tribological tests indicated significant improvements in wear resistance, with TiC and NbC coatings showing reductions in weight loss by 37% and 41%, respectively.
Results indicated that adding ZrO2 increased the microhardness of the coatings, with the highest hardness of 348 HV achieved at 10% ZrO2.
Researchers have developed high-entropy alloy composite coatings using laser cladding technology on martensitic stainless steel substrates, focusing on the CoCrFeMnNi-ZrO2 alloy.
The laser cladding process not only refines the microstructure but also achieves a uniform distribution of elements, which is crucial for enhancing the mechanical properties of the coatings.
These coatings feature a transition layer and a hard surface layer, with the latter containing a high concentration of spherical tungsten carbide particles.
The study investigates the optimization of tungsten carbide content in nickel-based coatings to balance hardness and wear resistance.
Among the findings, the FeNiCr + 3 wt.% NbC coating exhibited superior micromechanical properties, achieving an average microhardness of 3.8 GPa.
Electrochemical tests revealed a notable improvement in corrosion resistance for the composite coating compared to the substrate.
Finite element simulations showed that ZrO2 particles enhance resistance to cavitation erosion by withstanding higher stress and generating compressive stress on the coating surface.
Increased SiC content was found to prolong the initial wear stage and reduce the wear rate by delaying the breakdown of the oxide film.
The demand for materials with superior performance in harsh environments is driving the development of high-entropy alloys for applications in turbine blades and bearings.
High-entropy alloys possess unique properties attributed to effects such as high-entropy, lattice distortion, hysteresis diffusion, and the cocktail effect.
Summary based on 7 sources