EU Mandates Zero-Emission Cars by 2035, Boosting Electric Vehicle Adoption and Battery Recycling Innovation
December 23, 2024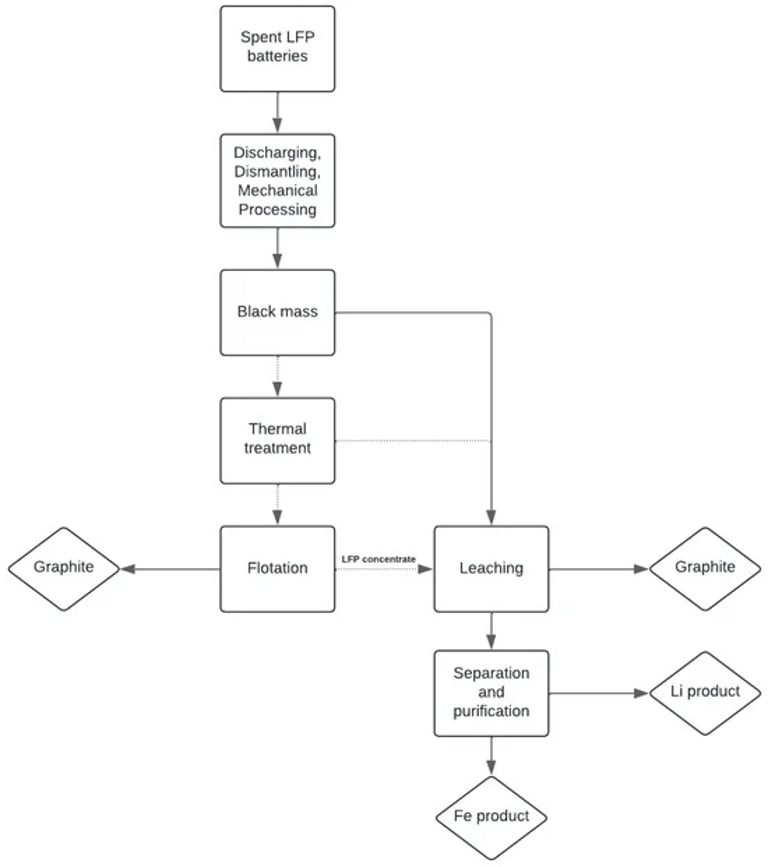
The European Union has set a mandate for zero-emission cars by 2035, which is expected to significantly boost the adoption of electric vehicles (EVs).
The transportation industry is rapidly transitioning from fossil fuels to electric vehicles, with Europe leading this charge; Norway notably achieved a remarkable 79% market share for EVs in 2022.
Projections suggest that by 2025, electric vehicles will dominate the market, with China targeting a 25% share.
Lithium-ion batteries (LIBs) are the preferred choice for EVs due to their high energy density and longevity, typically lasting between three to six years.
LIBs are categorized based on their cathode materials, such as nickel cobalt aluminum oxide (NCA) and lithium iron phosphate (LFP), with ongoing research focused on enhancing their efficiency and recyclability.
In China, LFP batteries have gained popularity, surpassing nickel cobalt manganese (NCM) batteries in market share in 2021, primarily due to their safety and cost advantages.
The typical composition of an LFP battery includes materials like carbon, lithium, and iron, highlighting the importance of developing effective recycling methods for spent lithium-ion batteries.
Hydrometallurgical methods are widely employed for recycling LIBs, utilizing leaching and purification processes to recover lithium and other valuable metals from spent batteries.
Studies on sulfuric acid leaching have shown high lithium recovery rates, particularly when oxidizing agents are used to enhance selectivity.
Various leaching methods have been explored, with sulfuric acid being favored for its cost-effectiveness and efficiency in dissolving lithium.
Precipitation studies indicate that while iron and phosphorus precipitate easily, lithium remains largely in solution across different pH levels, necessitating further purification techniques.
Thermal treatment of black mass from spent batteries is essential for improving flotation and hydrometallurgical processing by effectively removing binders and organics.
Flotation experiments have demonstrated that thermal treatment significantly enhances graphite recovery rates, with optimal conditions occurring around 450 °C for binder decomposition.
Summary based on 1 source